The electric vehicle controller is the core control device used to control the start, operation, advance and retreat, speed, stop of the electric vehicle motor and other electronic devices of the electric vehicle. It is like the brain of the electric vehicle and is an important part of the electric vehicle. At present, electric vehicles mainly include electric bicycles, electric two-wheeled motorcycles, electric tricycles, electric three-wheeled motorcycles, electric four-wheeled vehicles, battery cars, etc. Electric vehicle controllers also have different performances and characteristics due to different models.
The electric vehicle controller is a component that controls the speed of the electric motor and is also the core component of the electric vehicle system. Controllers generally have undervoltage detection, current limiting and overcurrent protection functions. The intelligent controller also has a variety of riding modes and the self-checking function of the electrical components of the whole vehicle. The controller is the core component of the electric vehicle energy management system and various signal processing. Its main function is to control the speed of the motor. In the electric vehicle industry, the controller is also required to have corresponding protection functions such as braking power-off, under-voltage protection, under-voltage recovery value setting, and over-current protection.
5 main functions of electric vehicle controller:
1. Drive the motor to rotate.
2. The motor drive current is changed under the control of the turning handle, so as to realize the adjustment of the motor speed.
3. Under the control of the brake handle (brake handle), the output current is cut off to realize the braking control.
4. Detect the battery voltage. When the voltage stored in the battery is close to the "discharge termination voltage", the controller panel (or instrument display panel) will display the insufficient power to remind the rider to adjust his travel. When the termination voltage is reached, The signal is sent to the comparator through the sampling resistor, and the protection signal is output by the circuit, so that the protection circuit sends an instruction according to the preset program to cut off the current to protect the charger and the battery.
5. Overcurrent protection, when the current is too large, the overcurrent protection circuit will act to stop the motor and prevent the overcurrent from causing harm to the motor and the controller. In addition, some controllers also have functions such as anti-speeding protection and cruise speed limit.
In order to prevent the controller from entering water and facilitate heat dissipation, the controller is installed in a sealed box made of aluminum, copper and other materials.
The design quality and characteristics of the electric vehicle controller, the function of the microprocessor used, the power switch device circuit and the layout of peripheral devices, etc., are directly related to the performance and operating status of the entire vehicle, and also affect the performance and efficiency of the controller itself. Different quality electric vehicle controllers, used in the same vehicle and equipped with the same set of batteries in the same charge and discharge state, sometimes show great differences in driving ability.
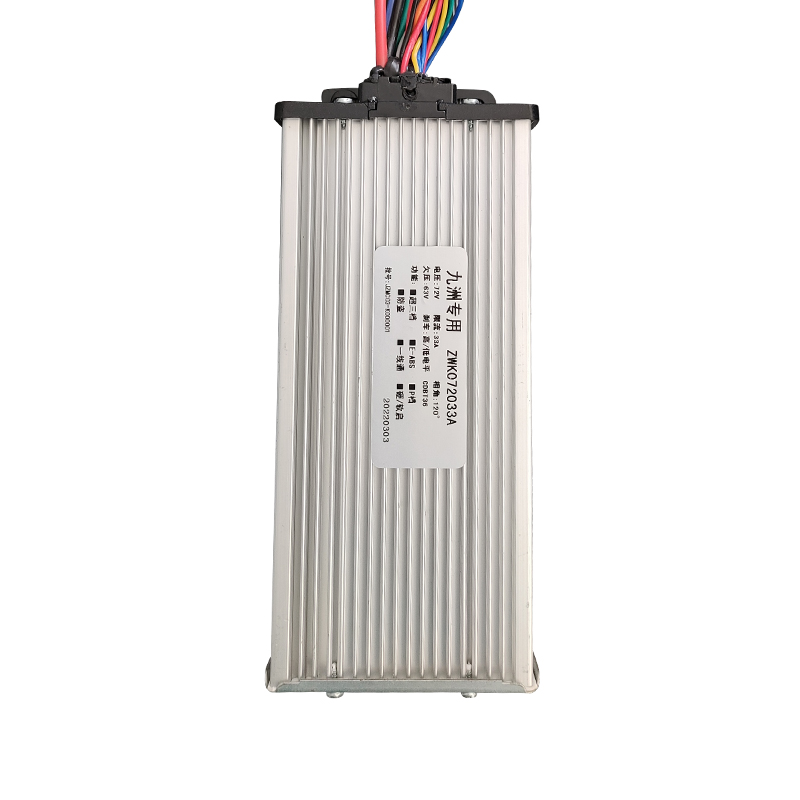
15 Tube wired Electric Moped controller
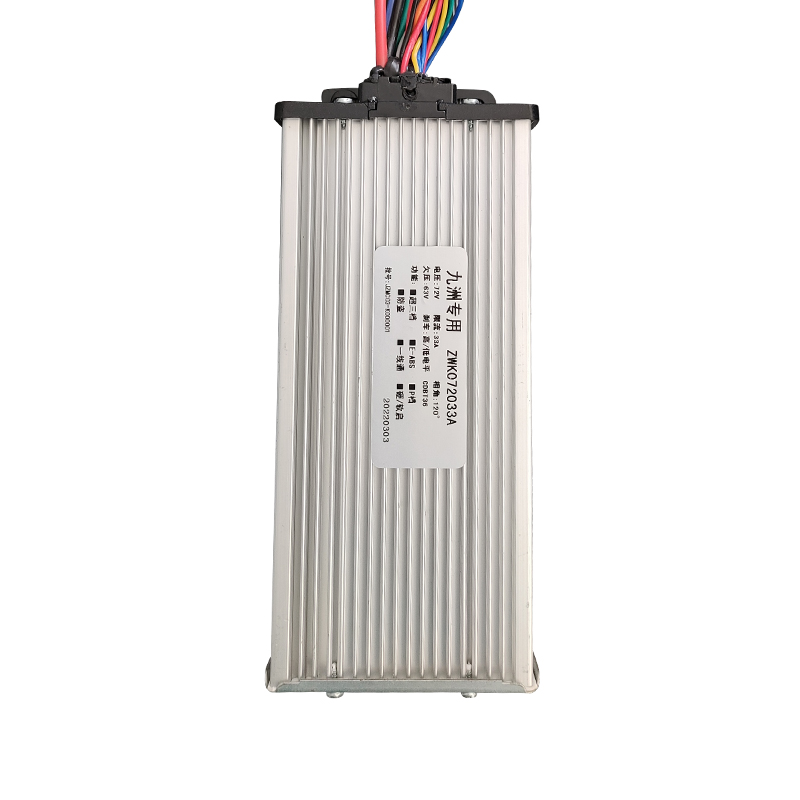
15 Tube wired Electric Moped controller
1. Full metal structure heat dissipation design to increase the heat dissipation area and effective shielding interference
2. Product interface rich optional RS485, Bluetooth, LIN, CAN bus, etc.
3. Software can support OTA over-the-air upgrade